QR Code
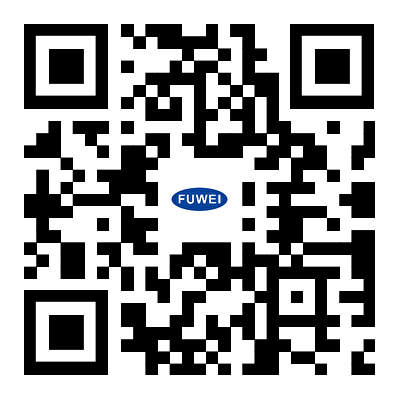
About Us
Products
Contact Us
Phone
E-mail
Address
No. 22, Hongyuan Road, Guangzhou, Guangdong Province, China
As the manufacturing industry accelerates towards greater precision and efficiency, higher requirements have been placed on the level of automation and intelligence in the production process. Faced with complex and highly precise workpieces such as inertial rings, traditional loading methods have become inadequate. At this moment, the rise of 3D vision technology has brought revolutionary solutions to this problem. It not only greatly improves the accuracy of feeding, but also significantly enhances the flexibility and efficiency of the production line.
The basic principle of 3D vision technology is to process and analyze the three-dimensional spatial information of objects through computers, and achieve operations such as object recognition, detection, tracking, and measurement. In the application of precise feeding of inertial rings, 3D vision technology captures the three-dimensional spatial information of the inertial ring, providing the robot with accurate grasping position and posture, thus achieving precise feeding of the inertial ring.
In terms of imaging algorithms, 3D vision technology adopts advanced algorithms to cope with complex situations such as surface reflection and oil film coverage of inertial rings. By optimizing algorithms, the system is able to generate clear and accurate point cloud data, providing a solid foundation for subsequent recognition and capture.
In terms of camera selection, 3D vision systems need to choose cameras with high resolution, large field of view, and large depth of field. This type of camera can capture the complete shape and size information of the inertial ring, ensuring that the robot can accurately find the target position during the grasping process. At the same time, the characteristic of large depth of field enables the camera to maintain clear imaging effects at different distances, further improving the accuracy of feeding.
In addition to imaging algorithms and camera selection, 3D vision technology also needs to be closely integrated with robot control systems. By transmitting real-time three-dimensional spatial information of the inertia ring to the robot control system, the robot can accurately locate the position of the inertia ring and perform grasping. This real-time information exchange enables robots to quickly adjust their grasping strategies when facing inertia rings of different specifications, achieving flexible production.
3D vision technology has played an important role in the precise feeding process of inertial rings. By optimizing imaging algorithms, selecting appropriate cameras, and closely cooperating with robot control systems, this technology achieves efficient and precise grasping of inertial rings, improves production efficiency, and reduces production costs.
No. 22, Hongyuan Road, Guangzhou, Guangdong Province, China
Copyright © 2024 Guangzhou Fuwei Electronic Technology Co., Ltd. All Rights Reserved.
Links | Sitemap | RSS | XML | Privacy Policy |