QR Code
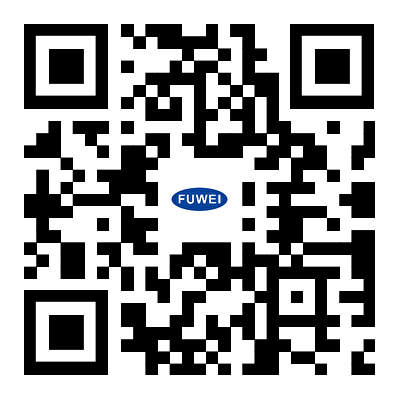
About Us
Products
Contact Us
Phone
E-mail
Address
No. 22, Hongyuan Road, Guangzhou, Guangdong Province, China
In modern manufacturing, the efficiency and intelligence of logistics processes have a crucial impact on production efficiency. A certain manufacturer decided to upgrade the traditional manual handling method to an intelligent solution when faced with high-intensity and fast-paced handling tasks. The original manual handling not only required a large amount of human resources, but also had a high intensity of repetitive operations and long distances, resulting in low work efficiency and chaotic on-site operation processes. Manufacturers hope to achieve the intelligent manufacturing goals of Industry 4.0 through intelligent transformation.
Solution
To address the above challenges, manufacturers have introduced AGV robots with lifting capabilities. The robot has a load capacity of 1000 kilograms, a navigation accuracy of ± 5 millimeters, a running speed of about 1.5 meters per second, a lifting height of 60 ± 2 millimeters, and can work continuously for 7.5 hours under full load. Its laser SLAM navigation technology provides 360 degree all-round safety protection and supports both automatic and manual operation modes.
Unique advantages of the solution
1. Intelligent scheduling and charging management: The AGV robot is equipped with an FMS scheduling system that can monitor the AMR's battery level in real time and issue an alarm or automatically start charging when the battery is low, ensuring that the robot is always in optimal working condition.
2. Efficient transportation flow optimization: Based on AMR vehicle management, traffic status, and transportation task instructions, the system can achieve efficient transportation flow optimization. Ensure smooth and efficient logistics processes through vehicle allocation, traffic control, and coordinated avoidance.
3. Automated cargo handling: AGV robots can automatically complete the handling, orderly placement, and inbound/outbound operations of goods according to warehouse planning, and seamlessly integrate with the three-dimensional warehouse management system to achieve comprehensive automated logistics management.
4. Multi system compatibility and integration: The system has rich interfaces and can interface with various material and warehouse management systems such as MES and IWMS. It supports connecting on-site sensor signals, automatic door switches, and elevator access signals, achieving multi-faceted information exchange and collaborative operations.
5. Centralized control and management: All AGVs and AMRs are centrally scheduled and managed by the "Fuwei Integrated Controller" to ensure efficient coordination and resource optimization among various devices.
6. Multiple safety protection measures: The system adopts multiple safety protection measures such as linear deceleration parking, automatic station parking, emergency parking (emergency stop button), laser collision avoidance (primary protection), and emergency braking (secondary protection) to ensure the safety of the working environment.
Application effects and prospects
By introducing AGV lifting robots, the manufacturer has not only achieved intelligent transformation of the logistics process, greatly improving work efficiency and safety, but also optimized the overall production process and reduced labor costs. This solution demonstrates the enormous potential of intelligent manufacturing in the Industry 4.0 era and provides valuable reference for other manufacturing enterprises.
With the continuous development and deepening of intelligent technology, the application prospects of AGV robots in the manufacturing industry will be even broader. In the future, AGV technology will continue to drive the development of manufacturing towards intelligence and automation, achieving more efficient and safer production management.
No. 22, Hongyuan Road, Guangzhou, Guangdong Province, China
Copyright © 2024 Guangzhou Fuwei Electronic Technology Co., Ltd. All Rights Reserved.
Links | Sitemap | RSS | XML | Privacy Policy |