QR Code
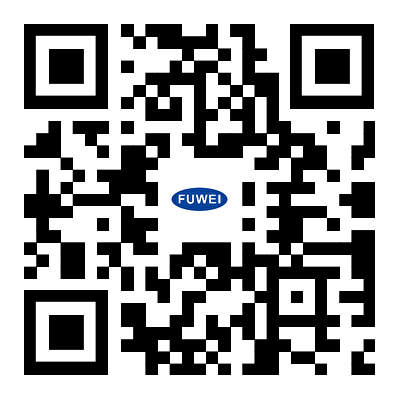
About Us
Products
Contact Us
Phone
E-mail
Address
No. 22, Hongyuan Road, Guangzhou, Guangdong Province, China
With the rapid development of intelligent manufacturing and industrial automation, the loading and unloading scheme of composite robots has become a key technology to improve production efficiency and reduce labor costs.
conceptual design
Requirement analysis: Firstly, it is necessary to conduct in-depth analysis of the loading and unloading requirements of the production line, including material types, sizes, weights, loading and unloading frequencies, etc., in order to provide accurate basis for subsequent scheme design.
Robot selection: Based on the results of demand analysis, select a suitable composite robot. Factors to consider include the robot's load capacity, accuracy, speed, stability, etc.
Design of loading and unloading device: Design a loading and unloading device that meets the requirements of robot grasping and placement, ensuring that materials can be accurately and quickly loaded and unloaded.
Control system design: Design a control system to achieve collaborative work between the robot and the loading and unloading device, ensuring smooth and efficient loading and unloading processes.
Implementation of the plan
On site investigation: Conduct an investigation of the production line site to understand the on-site environment, equipment layout, personnel operation, and other conditions, in order to prepare for the subsequent implementation of the plan.
Equipment installation and debugging: Install the composite robot and loading and unloading device onto the production line, and conduct detailed debugging to ensure stable and accurate operation of the equipment.
Control system integration: Integrate the control system with other equipment on the production line to achieve seamless integration between robots and the production line.
Employee training: Provide training on the loading and unloading scheme of composite robots for employees to improve their operational skills and safety awareness.
Plan optimization and upgrade
During the implementation of the plan, it is necessary to continuously optimize and upgrade the plan to adapt to changes in the production line and improve production efficiency. The content of optimization and upgrading may include upgrading robot software, improving loading and unloading devices, optimizing control systems, etc.
No. 22, Hongyuan Road, Guangzhou, Guangdong Province, China
Copyright © 2024 Guangzhou Fuwei Electronic Technology Co., Ltd. All Rights Reserved.
Links | Sitemap | RSS | XML | Privacy Policy |