QR Code
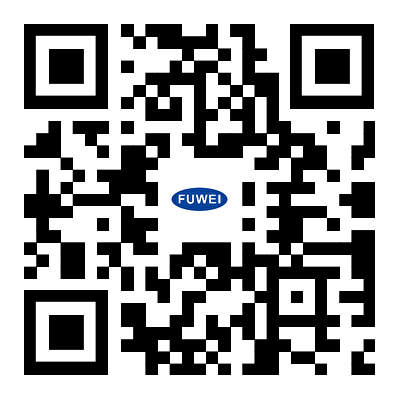
About Us
Products
Contact Us
Phone
E-mail
Address
No. 22, Hongyuan Road, Guangzhou, Guangdong Province, China
The rapid development of intelligent technology not only injects new vitality into traditional manufacturing, but also leads the industry towards a more efficient and intelligent future. Especially the implementation of CNC automatic loading and unloading scheme is undoubtedly a shining pearl in this innovation. With its unique advantages, it is quietly ushering in a new era of efficient production. This transformative technological breakthrough not only significantly improves the automation level of the production line, but also optimizes and upgrades the production process through precise control and efficient collaboration.
Project Background
Process Status
The production line workers manually assemble the products onto the fixtures, and then transport the fixtures along with the positioning table to the CNC machining equipment for product processing. After the CNC equipment is processed, the production line workers will remove the processed products from the CNC equipment and transfer them to the finished product placement area.
Process details
Product types: Multiple, but only with different placement table sizes. Placement table size: 140 * 160, maximum workpiece size 450 * 450 Product weight: 18kg
Zero point positioning station, this part is the same for all products
Vehicle connection block, all products have the same (gripping position) product placement platform, and the size of this part may not be the same for different products.
Docking requirement accuracy: ± 1.5mm. The processing time of each CNC equipment is about 4-6 hours
Program objectives
The composite robot automatically completes the "product handling" part of the production process according to the instructions of the production center. 1. The composite robot AMR can adjust the production status in real time according to the production center's plan. 2. It realizes the automatic confirmation of CNC machining completion by the composite robot AMR and the automatic transfer of finished products to the finished product placement area. 3. It determines the material preparation status of the loading area and automatically transfers the products to be processed to idle or processed CNC equipment.
Core advantages
1. The AMR composite robot achieves grasping error and placement error<± 1.5mm2
2. The composite robot AMR achieves automatic yielding when encountering vehicles, and stops automatically in the presence of pedestrians or obstacles; 3. The AMR composite robot is integrated with CNC equipment and can control the automatic opening and closing of the warehouse door during loading and unloading;
3. The success rate of AMR comprehensive placement for composite robots is over 99%;
Solution
Overall layout: 1. Configure two AMR composite robots for loading and unloading operations according to the on-site layout;
2. Complete trajectory operation through human-machine interaction signals and interaction signals between CNC machining centers and AMR composite robots; 3. The AGV car is equipped with a dedicated automatic charging station, which is expected to operate continuously for 7.5 hours at full load. It can be set to a battery level of less than 20% for early charging;
ForwardVision, a visual recognition software developed by Fuwei, can achieve high-precision recognition of Mark targets and output corresponding position information.
The recognition effect of this mark is only for illustration and does not represent the final mark style and recognition effect
Product Function Introduction
Charging method
Automatic charging:
The system monitors the AMR battery level in real time. When it falls below a certain threshold (which can be set by the customer), the system automatically schedules the AMR to locate the charging position, starts automatic charging, confirms the information, starts charging, and the device is in standby charging mode. If there is a task received, it will autonomously disconnect from charging and enter the working state.
Automatic charging is suitable for 24-hour long-term work projects
Manual charging:
The system monitors the AMR battery life in real-time. When it falls below a certain threshold (which can be set by the customer), the system automatically schedules the AMR to drive to the charging position, while providing sound and light prompts to remind personnel to charge it in a timely manner.
Communication docking method
The composite robot AMR receives instructions from the CNC and moves to the product library to grab products that have been manually assembled and confirmed through buttons. It then moves to the corresponding CNC equipment. At this point, the composite robot AMR sends a door opening request to the CNC equipment to wait for the cabin door to open and complete the material exchange. Afterwards, the composite robot AMR sends a signal to the CNC equipment to close the cabin door and start the equipment.
Hardware Introduction
FMS scheduling system
Detect the battery level of AMR, alarm or automatically charge when the battery level is low;
Efficient transportation flow optimization based on AMR vehicle management, traffic status, and transportation task instructions
Based on AMR vehicle allocation, traffic control, and coordinated avoidance, efficient transportation flow optimization is achieved;
Automated handling and organization of goods can be achieved according to warehouse planning, placement, inbound and outbound, etc
Can be integrated with the three-dimensional library management system to achieve automatic storage and retrieval;
Rich interfaces, 1 can interface with various material management systems, warehouse management IWMS, and more. Can interface with various physical systems. Like MES
Field I0 sensor signal
Such as material arrival signal, various automatic door switches for elevator exit, self entry, etc.
Product Function Introduction
Charging method
Automatic charging:
The system monitors the AMR battery level in real time. When it falls below a certain threshold (which can be set by the customer), the system automatically schedules the AMR to locate the charging position, starts automatic charging, confirms the information, starts charging, and the device is in standby charging mode. If there is a task received, it will autonomously disconnect from charging and enter the working state.
Automatic charging is suitable for 24-hour long-term work projects
Manual charging:
The system monitors the AMR battery life in real-time. When it falls below a certain threshold (which can be set by the customer), the system automatically schedules the AMR to drive to the charging position, while providing sound and light prompts to remind personnel to charge it in a timely manner.
Communication docking method
The composite robot AMR receives instructions from the CNC and moves to the product library to grab products that have been manually assembled and confirmed through buttons. It then moves to the corresponding CNC equipment. At this point, the composite robot AMR sends a door opening request to the CNC equipment to wait for the cabin door to open and complete the material exchange. Afterwards, the composite robot AMR sends a signal to the CNC equipment to close the cabin door and start the equipment.
Hardware Introduction
FMS scheduling system
Detect the battery level of AMR, alarm or automatically charge when the battery level is low;
Efficient transportation flow optimization based on AMR vehicle management, traffic status, and transportation task instructions
Based on AMR vehicle allocation, traffic control, and coordinated avoidance, efficient transportation flow optimization is achieved;
Automated handling and organization of goods can be achieved according to warehouse planning, placement, inbound and outbound, etc
Can be integrated with the three-dimensional library management system to achieve automatic storage and retrieval;
Rich interfaces, 1 can interface with various material management systems, warehouse management IWMS, and more. Can interface with various physical systems. Like MES
Field I0 sensor signal
Such as material arrival signal, various automatic door switches for elevator exit, self entry, etc.
No. 22, Hongyuan Road, Guangzhou, Guangdong Province, China
Copyright © 2024 Guangzhou Fuwei Electronic Technology Co., Ltd. All Rights Reserved.
Links | Sitemap | RSS | XML | Privacy Policy |