QR Code
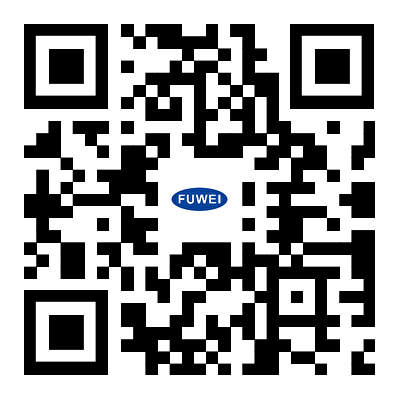
About Us
Products
Contact Us
Phone
E-mail
With the rapid development of industrial automation, traditional warehouse management models are no longer able to meet efficient and precise production needs. Especially in large production workshops, manual handling is not only inefficient, but also prone to errors, affecting production progress. We propose a warehouse handling solution based on a composite robot AMR (Autonomous Mobile Robot) and a handling robot AGV (Automated Guided Vehicle) to address this issue.
Customer pain points
The low efficiency of manual handling affects production progress.
Manual handling is prone to errors, leading to material confusion or loss.
The existing warehouse management system lacks intelligent and automated support.
Solution
1. System architecture
Our solution adopts a combination of composite robot AMR and handling robot AGV, combined with visual recognition system and FRDS intelligent scheduling system, to achieve automatic handling and management of materials in the warehouse.
2. AMR robot function
Complete basic warehouse location management functions, such as material inbound, outbound, inventory, etc.
Quickly and accurately locate materials based on simple instructions, and automatically complete handling tasks.
Complete instructions safely, efficiently, and reliably overall, reducing the need for manual intervention.
3. AGV robot functions
Responsible for transporting the material boxes of AMR robots to designated locations, such as production lines, three-dimensional warehouses, etc.
Equipped with elevator ride function, it can automatically trigger elevator requests and complete inter floor movements.
4. Visual recognition system
Responsible for scanning the code to confirm the information of the material box and the precise positioning of the material box in the warehouse location.
Cooperate with electric grippers to grasp the material frame and ensure stability during transportation.
5. FMS scheduling system
Detect the battery level of AMR, and sound an alarm or automatically charge when the battery is low.
Efficient transportation flow optimization based on AMR vehicle management, traffic status, and transportation task instructions.
It can be integrated with the three-dimensional library management system to achieve automatic storage and retrieval.
Rich interfaces that can interface with various material management systems, warehouse management systems, and on-site sensor signals.
Technical advantages
Efficiency: Through the collaborative work of AMR and AGV, the handling efficiency of materials in the warehouse has been greatly improved.
Accuracy: The visual recognition system ensures the precision of material handling and reduces error rates.
Intelligence: The FMS scheduling system realizes intelligent scheduling and management of AMR and AGV, improving the automation level of the system.
Flexibility: The system has high scalability and customizability, which can meet the actual needs of different customers.
Core values
Improving production efficiency: Through an automated handling system, the labor intensity and time cost of manual handling have been reduced, and production efficiency has been improved.
Reduce error rate: The high precision and intelligent management of the system effectively reduce the error rate during material handling.
Optimizing warehouse management: By integrating with the warehouse management system, real-time monitoring and efficient management of materials in the warehouse have been achieved.
Enhancing enterprise competitiveness: By improving production efficiency and reducing error rates, it helps to enhance the overall competitiveness and market position of the enterprise.
Copyright © 2024 Guangzhou Fuwei Electronic Technology Co., Ltd. All Rights Reserved.
Links | Sitemap | RSS | XML | Privacy Policy |