QR Code
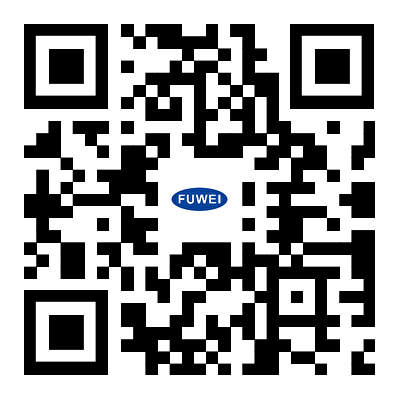
About Us
Products
Contact Us
Phone
E-mail
With the rapid development of the manufacturing industry, traditional manual loading and unloading methods are no longer able to meet the needs of efficient and precise production. Especially in the field of CNC machining, manual loading and unloading not only have low efficiency, but also pose safety hazards and accuracy issues. For this purpose, we have designed an automatic loading and unloading solution based on the composite robot AMR for a CNC machining production line of a manufacturing enterprise.
Process Status and Requirements
The current CNC machining production line of the enterprise adopts manual loading and unloading methods. Workers need to assemble the products onto the fixtures, and then transport the fixtures together with the positioning table to the CNC equipment for processing. After processing is completed, workers will remove the product and transfer it to the finished product area. This method not only has high labor intensity and low efficiency, but is also easily affected by human factors, leading to unstable machining accuracy.
Enterprises hope to achieve automated loading and unloading of CNC machining production lines, improve production efficiency, reduce labor intensity, and ensure machining accuracy.
Solution
Composite Robot AMR: Two AMR composite robots are used for loading and unloading operations, with high-precision grasping and placement functions, and can achieve seamless docking with CNC equipment.
Visual recognition system: Using Forward Vision visual recognition software, high-precision recognition of Mark markers is carried out to ensure the accuracy of robot grasping and placement.
Automatic Charging System: The AMR robot is equipped with an automatic charging station that monitors the battery level in real-time and automatically schedules charging, ensuring 24-hour continuous operation capability.
Communication docking method: The robot and CNC equipment communicate through dedicated signals to achieve automatic door opening, closing, and equipment startup operations.
FRDS scheduling system: Efficient scheduling and management of the entire production line to ensure collaborative operation between robots and CNC equipment.
Advantages of the plan
Efficiency: The composite robot AMR can achieve fast and accurate loading and unloading operations, greatly improving production efficiency.
Accuracy: By using visual recognition system and high-precision grasping technology, the product placement error is ensured to be less than ± 1.5mm, meeting the requirements of high-precision processing.
Safety: Robots have functions such as automatic obstacle avoidance and pedestrian detection to ensure safety during the production process.
Flexibility: The system can adjust the production status in real-time according to the production center's plan, adapting to the processing needs of different products.
Reliability: The comprehensive placement success rate of AMR robots has reached over 99%, ensuring the stable operation of the production line.
Implementation effect
By implementing this solution, the CNC machining production line of the manufacturing enterprise has achieved automated loading and unloading operations, increased production efficiency by more than 30%, and significantly improved product processing accuracy. At the same time, it reduces the labor intensity and safety risks of workers, bringing significant economic and social benefits to the enterprise.
This case demonstrates the application effect of CNC automatic loading and unloading solution based on composite robot AMR in the manufacturing industry. With the continuous development of intelligent manufacturing technology, we believe that in the future, more enterprises will adopt automated and intelligent production methods to improve production efficiency, reduce costs, and enhance product quality. We will continue to monitor market trends and technological developments to provide high-quality intelligent manufacturing solutions for more enterprises.
Copyright © 2024 Guangzhou Fuwei Electronic Technology Co., Ltd. All Rights Reserved.
Links | Sitemap | RSS | XML | Privacy Policy |